Mastering the Art of SMT Assembly: Tips for Success
With time, technology is getting advanced and as a result, electronic designs are getting smaller and more complicated. Since 1980s the engineers have relied on surface mount technology for PCB assembly. Many electronic devices or digital devices that we use in our daily routine including smartphones, have been made through surface mount technology. Let us move towards the basics of SMT assembly.
In surface mount technology, PCB components are placed directly on the board without drilling any holes. This technology is preferred by experts to through-hole technology. In contemporary electronics, this is the type of electronic component packaging that is most frequently employed.
It has several advantages over traditional through-hole technology. For example, it is lighter in weight, and cheaper in cost. It is better in performance and is automated.
SMD Components for SMT Assembly
It is very important to know what type of components should be used in the SMT assembly as they make the core of any SMT assembly service. SMD components or Surface Mount Devices are electronic components for SMT.
The components are available in a variety of sizes and packaging which includes transistors, resistors, integrated circuits (ICs), diodes, and capacitors.
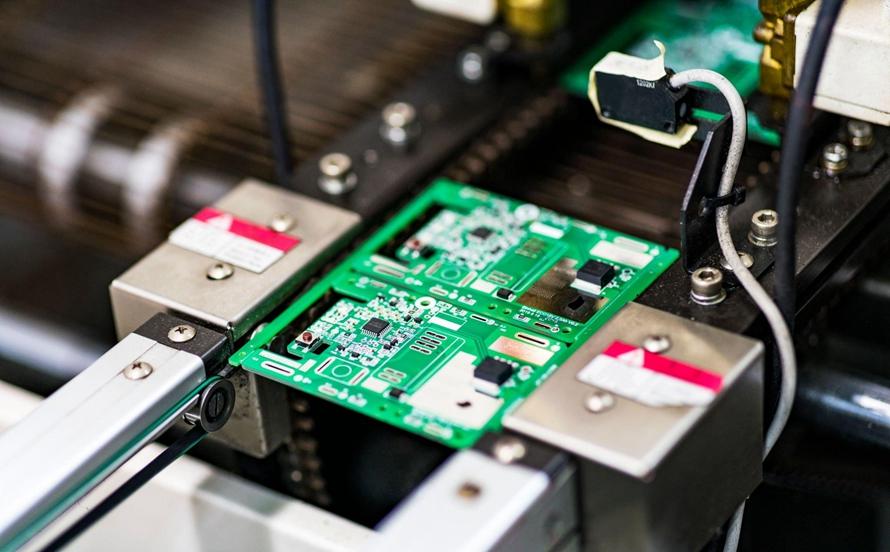
From the minuscule 01005 packages (about 0.4 x 0.2 mm) to the more considerable packages like a quad flat package (QFP), various sizes are available. The end product would be affected by each component and size.
What Are the Initial Steps Involved in the SMT Assembly
As SMT does not require PCBs to have holes drilled in them, it is more appropriate for mass production, unlike through-hole technology. We will examine many SMT Assembly techniques and how to be successful in this field in this article.
Screen Printing
In the SMT assembly process, the 1st stage is to prepare the circuit boards and the preparation of surface mount components (SMCs). The PCBs are usually made with copper layers and covered with solder masks to prevent the problem of a shortage of copper tracks during the production process. Particularly the SMCs come in reel packaging and are supplied in tapes.
Component Placement in PCB Design & Assembly
Next on the steps is the right placement of the components on the board as per the design specifications. It is done with the help of a pick-and-place machine.
To place the components right on the board the machine uses the vacuum nozzle to extract the components from reel packaging. The machine is capable of making sure the components are placed correctly on the board.
Reflow Soldering
The next step is the reflow soldering, during this stage, the reflow soldering oven is used to melt the paste which makes a strong connection between the components and the printed circuit board. The temperature of the oven is maintained in such a way that it guarantees the complete heating and melting of the paste to make the connection. The oven is usually placed behind the mounting machine in the SMT PCB assembly line.
There are different heating zones in this stage. The first is the pre-heating zone. At first, the temperature reaching 140-160 degrees Celsius is maintained for about 1 to 2 degrees per second and then the same temperature in the soak zone is maintained for 60 to 90 seconds.
After that, the board enters the reflow zone where the maximum temperature of 210 to 230 degrees is maintained to melt the solder paste. The last step in this stage is the cooling process. If you want to make sure that there are no connection problems you have to make sure older paste correctly after it leaves the heating zone. Note that if the board has multiple layers then the process may be repeated to cover all layers.
Inspection and Quality Control
The next, important step in the SMT assembly is the inspection of the final product. It can be done manually or with the help of different technologies like automated optical inspection or X-ray inspection. You can check the final board manually with the help of a magnifying glass or with the naked eye. But for more precise results machines are preferable.
For this, automated optical inspection (AOI) devices are frequently being used. With the use of side- and downward-facing cameras, AOI machines can examine the PCB and detect typical soldering problems such as tombstoning, solder bridging, raised pins, and inadequate solder or gaps. To find soldering issues, engineers can also visually analyze the soldered areas in SMT PCB assembly.
Rework if Needed
After the inspection, if any defect is identified then it has to be reworked and has to go through all the steps again. The fundamental tools like soldering iron and rework station could be placed in any location in the assembly line.

Best Practices You Should Adopt for SMT Assembly
To excel in SMT PCB assembly manufacturers have to take care of the following things.
Manufacturing Design
To maximize the efficiency of production and to reduce risk the manufacturer should make sure that the design of the PCB is suitable for SMT assembly. It is an important step in the process and it can’t be neglected.
Component Selection
Component selection matters in SMT assembly. If you want perfection in SMT assembly then you have to make sure that you choose the right components for the desirable products. You have to keep in mind the factors like size of the packaging and thermal characteristics.
Quality Control
You have to make sure that you follow up with quality control measures at different stages of the production process. There are different measures as we have discussed earlier such as X-rays and AOI.
Rework and Repair System
Let’s consider there is a defect in the end product then to address the defect or any issue you should have the best rework or repair system to get the best quality.
Training and Skills Development
Training and skills development of the staff members play an important part in SMT assembly. The more skilled they are, the better quality products they can produce. It also lowers the error rates and increases the yield rates.
Conclusion
With the help of SMT technology, you can make devices that are small and lighter in weight. SMT technology makes the manufacturing process easy and simple and reduces the chances of human errors.
This is specifically important for complicated circuits. The manufacturers could excel in the SMT assembly by understanding the different methods and by overcoming the challenges they face during the whole PCB assembly.
See Also: Unlocking The Full Potential: Maximizing Value From Your Used Car Purchase