Before the digital revolution organizations were primarily depending on institutional knowledge for the maintenance of equipment. With the advent of fault detection and diagnostics technologies, companies can now have the knowledge to be algorithmically utilized, shifting from a reactive maintenance approach to predictive maintenance.
Currently, a lot of buildings are adopting FDD technology to become intelligent buildings. Fault detection diagnostics is mandatory for a smart building to operate efficiently. It detects flaws in the system and notifies the management to make necessary changes. In some cases, the AI automated systems can make changes automatically with pre-set instructions from FDD systems.
FDD Systems: A Deeper Look
While understanding the historical shift in maintenance approaches is crucial, it’s equally important to delve into the mechanics that power these advanced FDD systems. Let’s explore the technology behind the scenes.
FDD tools use an advanced Fault Rules Engine that calculates fault probability and associated costs, integrating seamlessly with popular building automation systems (BAS), supervisory control and data acquisition (SCADA), programmable logic controllers (PLC), and other monitoring systems.
Now that we’ve uncovered the technical prowess of FDD, it’s time to address the pressing question: What tangible benefits do these systems bring to the table? The numbers might surprise you.
Organizations using FDD across 550 buildings achieved median savings of 8%. Data suggests that 5%–30% of commercial building energy is wasted due to control-related issues. These statistics highlight the undeniable advantages of FDD, from energy savings to improved operational efficiency.
Impressive as these benefits are, one might wonder how they function across different industries. Whether it’s the automotive sector or the pharmaceutical world, let’s see how fault detection diagnostics (FDD) is making waves.
FDD Across Various Industries
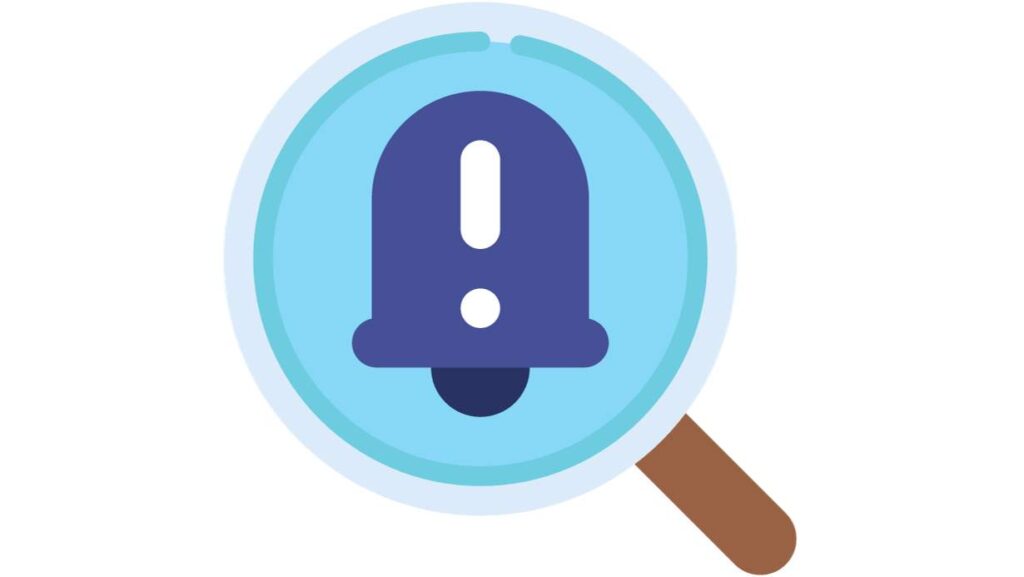
New FDD algorithms are continuously being developed, along with the rise in software, data availability, and data analytics in the building industry. The market now offers dozens of full-featured FDD software product offerings that integrate with building automation systems or can be retrofitted add-ons to existing equipment.
Automotive
Fault detection and diagnostics (FDD) offers immense value in the automotive sector. It allows manufacturers to be predictive in maintenance models for assembly line equipment. Sophisticated FDD systems analyze sensor data from machines to identify anomalies and detect potential failures before they occur. This prevents costly unplanned downtime and production bottlenecks. With early warning, maintenance can be scheduled efficiently during planned outages.
It generates a prioritized list of maintenance tasks based on its present state, allowing technicians to optimize their time. Helps them plan which equipment they need to handle the maintenance, such as a lift to reach specific heights for better support. Vital repairs get addressed quickly while less critical issues can wait. By leveraging predictive capabilities, manufacturers reduce unnecessary maintenance tasks and are able to focus on more important issues. Maintenance efforts become more proactive.
FDD also facilitates compliance with safety and emissions regulations in auto factories. Abnormal emissions can be caught early to prevent environmental violations.
The benefits translate across the production process – from stamping and welding to painting and final assembly. FDD-driven predictive maintenance is becoming an indispensable tool for maximizing uptime and efficiency in auto manufacturing buildings.
Pharmaceutical
In the pharmaceutical industry, FDD plays a crucial role in minimizing product waste due to equipment malfunctions and enhancing product quality by enabling predictive maintenance. Pharmaceutical manufacturing involves highly sensitive instruments where even minor performance drifts can negatively impact drug quality and batch yields if not detected early.
FDD software uses the current performing rate of the equipment to analyze that data, which is used to predict the future performance of equipment. This prevents millions in losses from discarded batches. FDD also helps pharma companies comply with stringent regulatory requirements regarding equipment maintenance and performance monitoring. By keeping a close eye on the equipment’s health, pharmaceutical manufacturers can optimize quality control.
Sustainability
FDD supports sustainability efforts in various ways. Reducing avoidable maintenance tasks lowers the environmental footprint associated with maintenance activities. Unnecessary technician trips and equipment handling are minimized. FDD also prolongs equipment lifetime by enabling timely repairs, reducing the waste produced when assets fail prematurely.
With more efficient operations achieved through predictive maintenance capabilities, organizations further lower their environmental impact. Energy savings from well-tuned equipment also support sustainability goals. Overall, the transition from reactive maintenance to predictive maintenance powered by FDD software allows organizations to operate in a more sustainable manner.
Utilities and Energy
For electric, gas, and water utilities, fault detection and diagnostics (FDD) delivers immense value by enhancing maintenance strategies for extensive transmission and distribution assets. Advanced FDD analytics leverage IoT sensor data and equipment logs to identify anomalies in generators, turbines, transformers, pumps, and other assets. Utilities can detect issues proactively and schedule maintenance during planned outages, avoiding unplanned downtime.
Prioritized maintenance lists also optimize technician time and resources on the most critical repairs. Predictive insights support strategic decisions about asset health and remaining useful life. By reducing reactive tasks, utility equipment technical staff can focus on higher-value responsibilities to serve customers better. FDD is becoming integral to predictive maintenance in capital-intensive utility operations.
Oil & Gas
In the oil and gas industry, unexpected outages caused by equipment failure can cost companies millions in lost production. By applying FDD techniques, issues can be flagged before they cause shutdowns. FDD systems aggregate and analyze sensor data across rigs, refineries, and pipelines to detect anomalies predictive of failure. With early diagnosis, repairs can occur during planned maintenance periods. Costly unplanned downtime is minimized.
Oil and gas companies can also leverage FDD insights to optimize maintenance scheduling. This ensures assets stay operational to keep production and distribution steady. FDD is becoming essential for productivity in the fast-paced, high-uptime oil and gas sector.
Building Automation
For facilities managers, FDD improves building automation by providing granular insights into HVAC, lighting, security, and other systems. Facility teams are instantly notified of faults so issues can be quickly diagnosed and addressed. FDD analytics help track equipment degradation and predict impending failures before they cause service disruptions. This shift from reactive to proactive maintenance enhances tenant comfort and productivity.
With a deep vision of daily operations, facility teams can optimize maintenance scheduling and make data-driven decisions about capital upgrades. FDD technology unlocks immense value in building automation.
Conclusion
In summary, FDD software has transformed equipment maintenance from a reactive undertaking to a proactive strategy powered by predictive analytics and fault diagnostics. Organizations that implement FDD solutions can expect decreased downtime, extended asset life, improved sustainability, and significant cost savings. By enabling predictive maintenance, FDD gives companies the insights they need to operate more efficiently. The use cases across industries demonstrate the immense value of these tools. Any operation that manages critical equipment should consider integrating fault detection and diagnostics capabilities.
FAQs
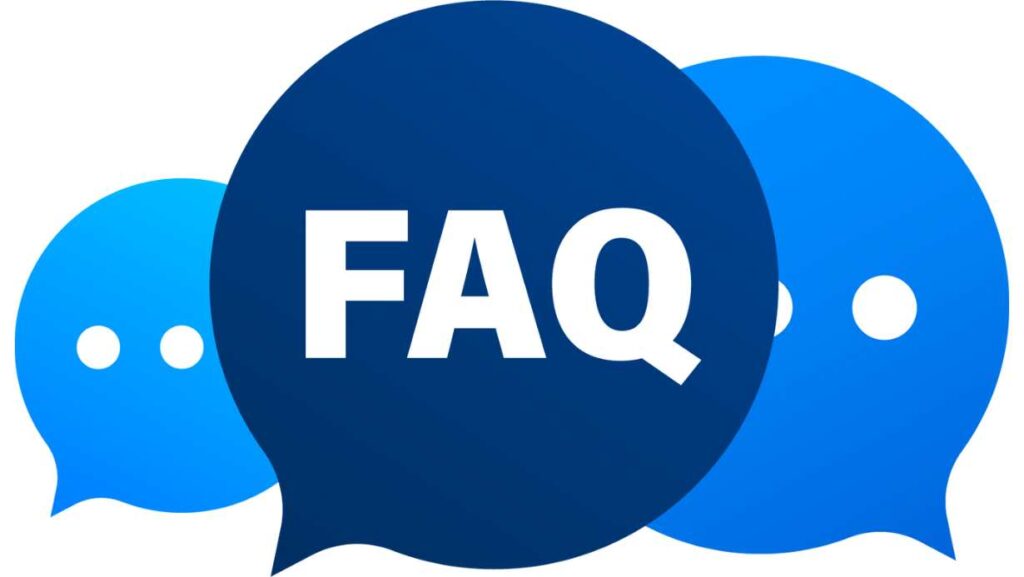
How does FDD software differ from traditional maintenance approaches
FDD utilizes predictive analytics rather than relying on reactive and time-based maintenance. By monitoring equipment performance, it identifies issues before they become problems. This reduces downtime and lowers costs.
Can FDD software integrate with existing monitoring systems in an organization?
Yes, most FDD solutions can integrate with common platforms like BAS, SCADA, and PLC. Many also provide open APIs for custom integration. This allows organizations to build on current infrastructure.
What is the typical ROI period for implementing FDD solutions?
Most organizations see a return on their FDD investment within 12 to 18 months. The savings come from reduced equipment downtime, fewer maintenance needs, and optimized operational efficiency.
See Also: Predictive Dialing vs Manual Dialing: Which Is More Efficient?